INTRODUÇÃO AOS DUTOS
Dutos têm sido usados há centenas de anos para transportar recursos de um local para outro. Desde tubos básicos de madeira amarrados em comprimentos, até modernos tubos de cloreto de polivinil não plastificado (uPVC – PVC rígido), eles sempre desempenharam um papel fundamental na sobrevivência humana. Essas seções tubulares fabricadas agora podem ser encontradas em todos os lugares do planeta desempenhando inúmeras funções essenciais, desde transportar o esgoto de nossas casas, até os postes de iluminação publica.
Um dos setores que mais utiliza dutos é o setor de energia. Uma crescente população mundial demanda enormes recursos da indústria para apoiar esse crescimento. No entanto, as preocupações ambientais têm colocado todas as indústrias sob holofotes. À medida que aumenta a temperatura média da Terra, ou seja, o aquecimento global, como é mais comumente conhecido, se torna cada vez mais importante, a pressão para reduzir a pegada de carbono do setor de energia é um tema frequente de discussão entre líderes mundiais e a população em geral.
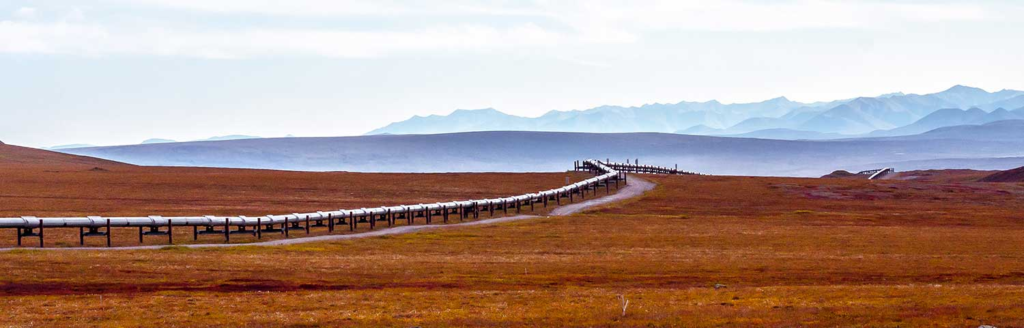
Apesar de todo olhar negativo que o setor de energia recebe, um grande esforço é dedicado para garantir que os milhões de quilômetros de dutos utilizados pela indústria atendam a rigorosos padrões de segurança, tanto em termos de produção dos próprios dutos quanto do produto transportado.
Este artigo analisa a produção dessas tubulações e examina a multiplicidade de técnicas usadas para instalar, manter e utilizar dutos em ambientes de trabalho modernos.
FABRICAÇÃO DE DUTOS
A forma oca e tubular dos dutos é inerentemente resistente e, portanto, adequada não apenas para suportar cargas externas na construção, mas também para transportar um produto de um lugar para outro. Quando você usa transporte público, liga o aquecimento, ar condicionado ou enche um copo com água, provavelmente está utilizando uma tubulação de alguma forma.
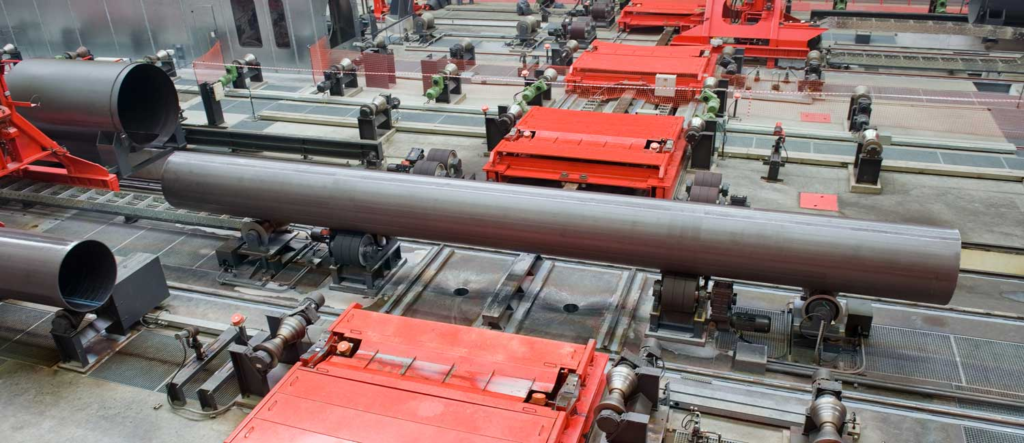
Atualmente, a maioria dos tubos é fabricada em usinas siderúrgicas. O uso de tubos de aço e sua fabricação remontam ao século XIX. Outros materiais, como ligas exóticas e agora o aço carbono, estão se tornando mais comuns. Embora o aço seja usado principalmente devido à sua resistência, ele também pode ser transformado em seções de tubos incrivelmente leves para uso em casos onde o peso do tubo é uma consideração, por exemplo, na fabricação de equipamentos de lazer ou quadros de bicicletas de corrida.
Os tubos de aço são tipicamente fabricados em dois tipos principais:
Tubo sem costura: feito perfurando um bloco sólido de aço para criar um tubo oco.
Tubo soldado: feito pegando uma chapa de aço e dobrando-a em forma de tubo.
Processo de fabricação de tubos sem costura
Este processo utiliza um perfurador rotativo para fazer um furo em um bloco sólido de aço que foi aquecido em um forno rotativo para tornar o material suficientemente macio para ser penetrado. O bloco de aço aquecido é então movido para o mandril com a ajuda de um conjunto de rolos e empurrado ao longo do comprimento, produzindo um tubo sem costuras.
Processo de fabricação de tubos soldados
A soldagem de chapas de metal em forma tubular por um processo de forjamento remonta a mais de 150 anos. Na verdade, o comerciante britânico de ferro, James Whitehouse, obteve uma patente já em 1825 para tubos soldados. Hoje, o aço com espessura de até 114 mm pode ser curvado em tubos, muitas vezes usando corrente elétrica para aquecer e preparar o material para a curvatura ou outras técnicas de fabricação de tubos.
TIPOS DE TUBULAÇÕES
Os dutos no setor de petróleo e gás são geralmente divididos em duas categorias:
- Transporte de líquidos
- Transporte de gás natural
Os de líquidos transportam produtos como petróleo bruto de sua localização de origem para a refinaria, onde será submetido a processos de produção, como a destilação.
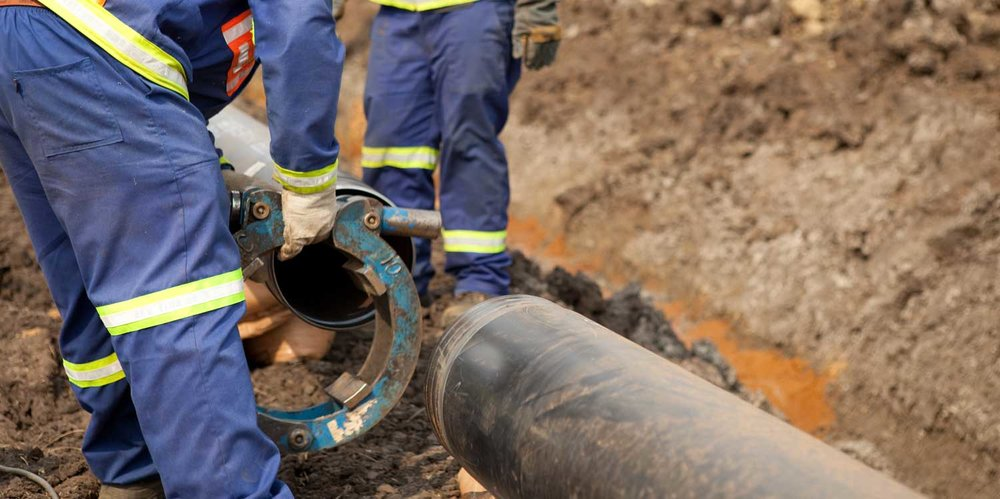
No entanto, os gasodutos transportam o produto da fonte para as plantas de processamento, onde serão distribuídos por meio de outra rede de dutos.
Dentro das duas principais categorias de dutos, existem 4 subcategorias:
1. Dutos de coleta: transportam petróleo bruto, gás natural e outros líquidos em curtas distâncias. Seu propósito geralmente é coletar produtos de fontes antes de levá-los para a próxima etapa de processamento.
2. Dutos de alimentação: transportam óleo, gás e outros líquidos de tanques de armazenamento e instalações de processamento para a próxima etapa – os dutos de transmissão.
3. Dutos de transmissão: transportam gás natural, líquidos, petróleo bruto e outros produtos processados por longas distâncias, onde os destinos podem estar em até em outros países.
4. Dutos de distribuição: esses dutos são usados para distribuir produtos diretamente para os clientes finais.
Os tubos podem variar em comprimento, mas normalmente têm 12 metros de comprimento. Eles podem ser cortados no tamanho desejado por uma equipe de produção em uma fábrica ou soldados em comprimentos mais longos para facilitar a instalação em campo.
As extremidades dos tubos são referidas como:
Extremidades lisas (PE)
Extremidades rosqueadas (TE)
Extremidades chanfradas (BE)
Tubos de extremidades lisas são comumente usados em tubos de pequeno diâmetro e conectados com flanges ou soldas.
Tubos de extremidades rosqueadas são também usados em conexões de tubos de menor diâmetro utilizando outros tubos rosqueados.
Tubos com extremidades chanfradas são geralmente soldados em comprimentos para criar redes com emendas quase imperceptíveis para o transporte do produto.
Os diâmetros dos tubos variam de acordo com a aplicação e o produto a ser transportado, mas geralmente podem ser categorizados da seguinte forma:
Tubos de diâmetro grande: 26″ – 60″ (66 cm – 152,4 cm)
Tubos de diâmetro médio: 14″ – 24″ (35,5 cm – 61 cm)
Tubos de diâmetro pequeno: 1″ – 12″ (2,5 cm – 30,5 cm)
O tamanho nominal do tubo (NPS) é o padrão norte-americano para tubos que são usados em altas ou baixas temperaturas ou pressões.
As dimensões dos tubos e suas medições serão abordadas em maiores detalhes posteriormente neste guia.
DUTOS E O MEIO AMBIENTE
Os oleodutos e gasodutos são frequentemente utilizados para transportarem produtos por longas distâncias, muitas vezes atravessando territórios de outro países. As consequências de um rompimento ou vazamento destes dutos podem ser potencialmente catastróficas. Portanto, para garantir a instalação, gestão e produção seguras de um oleoduto ou gasoduto, é necessário que as empresas de instalação sigam padrões rigorosos.
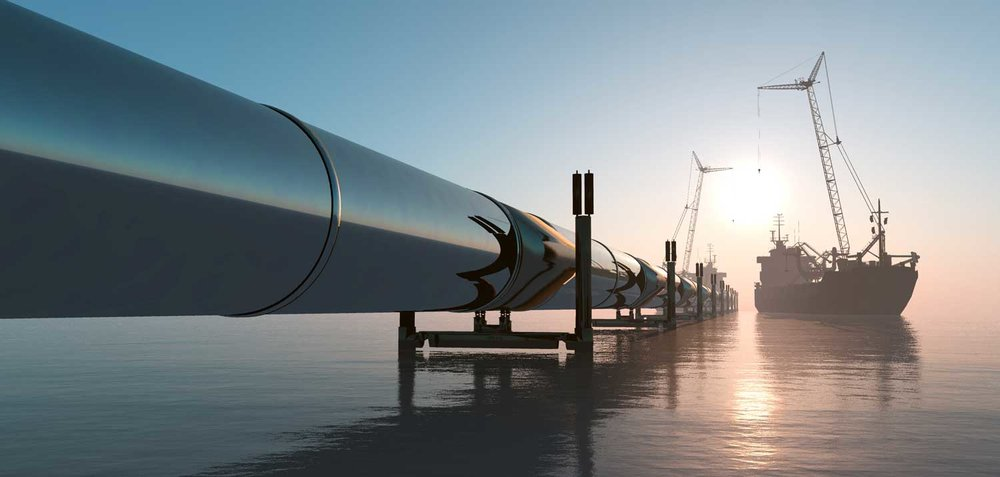
Antes da instalação, são levados em consideração diversos aspectos de sua construção, incluindo a rota, o entorno e o impacto resultante no meio ambiente. Frequentemente, há sensibilidades em relação à natureza do produto a ser transportado devido aos riscos envolvidos. A crescente conscientização ambiental tem levado o foco as atividades industriais que possam comprometer seres humanos, animais ou a própria natureza. Os produtos transportados por oleodutos e gasodutos são tipicamente corrosivos, inflamáveis e tóxicos, representando um risco para a vida.
Houve uma série de desastres recentes relacionados à indústria de óleo e gás, resultando em eventos catastróficos. Da mesma forma que a indústria da aviação adota uma resposta meticulosa a acidentes aéreos na tentativa de evitar sua repetição, o setor de petróleo e gás também reage de forma positiva.
A partir desses eventos desastrosos, a melhoria da segurança foi destacada, com grandes investimentos sendo realizados para minimizar riscos e melhorar a segurança em todas as áreas da indústria. Cada acidente agora leva a intensas revisões de segurança, em que processos, práticas, tecnologia e equipamentos são considerados.
FABRICAÇÃO E INSTALAÇÃO DE TUBOS
A fabricação de tubos é uma parte essencial na preparação de um oleoduto ou gasoduto para que esteja pronto para a produção. A fabricação de tubos pode envolver uma série de atividades, tais como:
Pintura
Revestimento interno
Curvatura
Corte
Soldagem
Codificação
Testes
Cada uma dessas técnicas de fabricação pode ser aplicada dependendo da natureza do produto que será transportado e da localização da instalação do duto.
Fabricação de dutos
Em certos cenários, como em águas profundas, por exemplo, é necessário que um duto não tenha apenas paredes espessas, seja forte e resistente, mas também seja resiliente a pressões intensas. Algumas dessas instalações de dutos estão em profundidades de milhares de metros, onde o risco de dobramento dos tubos é alto. Portanto, a fabricação e os testes são necessários para determinar se o tubo escolhido suportará o estresse e a pressão durante a operação.
Esses desafios não se limitam apenas aos tubos durante a fase de produção, mas também durante a instalação. As questões práticas de mover e construir uma rede de dutos em tais profundidades não apenas incluem garantir que as especificações rigorosas de instalação sejam atendidas, mas também cumprir as regulamentações de conformidade com a segurança, o que representa uma tarefa imensamente desafiadora para as empresas do setor.
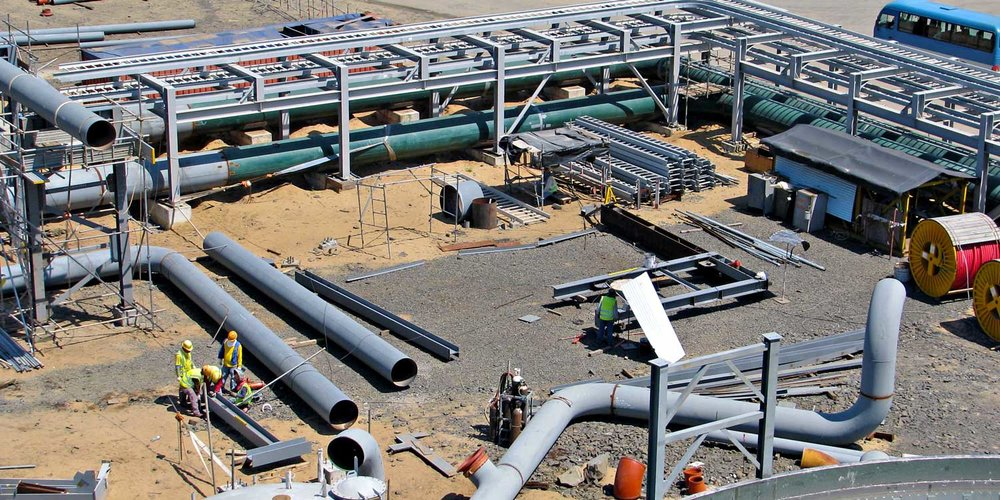
Por outro lado, a fabricação e construção de dutos para uso em terra é consideravelmente menos complexa. Embora esse tipo de instalação de dutos também apresente seus próprios desafios, atividades como transporte, montagem e construção são menos complicadas e também eliminam a necessidade de altos níveis de fabricação. Em instalações offshore, onde dutos de águas profundas são construídos usando métodos como tow-in, J-lay ou S-lay, são necessárias embarcações especializadas.
Instalação de dutos
Um processo padrão de instalação de dutos envolverá as seguintes etapas:
- Levantamento do local designado para instalação
- Planejamento, projeto e aprovação da rota
- Preparação do terreno
- Fabricação do material do duto
- Organização e dobra dos dutos para se adequarem à rota
- Soldagem das seções
- Inspeção e aprovação das juntas soldadas
- Revestimento das juntas
- Movimentação do duto para a posição adequada
- Instalação das válvulas
- Testes finais e aprovação
Projetos de instalação de dutos podem levar de alguns meses a vários anos para serem concluídos e requerem diversas habilidades diferentes, frequentemente implementadas por uma cadeia de suprimentos de empresas maiores. A inspeção independente e a subsequente aprovação por uma organização terceirizada na cadeia de suprimentos é benéfica para essas grandes empresas, pois adiciona um nível de rigor a um projeto, algo que não é alcançado quando eles aprovam seu próprio trabalho.
PADRÕES DE INSTALAÇÃO DE DUTOS
A instalação segura e o gerenciamento contínuo de dutos exigem que as empresas sigam rigorosos níveis de padrões durante as fases de construção e operação de um projeto de duto. Existem 3 principais códigos que os operadores de dutos devem observar:
Instituto Americano de Petróleo (API)
Organização Internacional de Normalização (ISO)
Cada uma dessas organizações estipula requisitos muito específicos para que os operadores reconheçam e incorporem em suas práticas de trabalho, tudo com o único objetivo de melhorar a segurança durante as fases de instalação e operação. Outro aspecto altamente importante é fornecer um padrão comum que seja aprovado pelos operadores de dutos e usado por subcontratados em projetos, incluindo as usinas de fabricação de dutos.
Códigos de prática da DNV
A Det Norske Veritas emitiu seu primeiro código de dutos em 1976 e desde então obteve reconhecimento global como administradora de uma das principais organizações de padrões de dutos. A DNV afirma que mais de 65% de todos os projetos concluídos seguem seus padrões. Estes compreendem especificações de serviço e práticas recomendadas, altamente respeitadas no setor internacional de dutos.
Padrões da API
Estabelecido em 1919, o Instituto Americano de Petróleo emitiu mais de 700 padrões para estabelecer, manter e distribuir padrões para a indústria de petróleo e gás. O objetivo da API é melhorar a segurança operacional, a proteção ambiental e a sustentabilidade em toda a indústria. Eles afirmam ajudar a acelerar a aceitação de projetos, levar produtos ao mercado mais rapidamente e evitar processos repetitivos toda vez que um produto é fabricado.
Organização Internacional de Normalização
A ISO oferece numerosos padrões em uma ampla variedade de organizações, mas também especifica e recomenda códigos de prática para o design, materiais, construção, testes, operação, manutenção e abandono de sistemas de dutos usados para transporte nas indústrias de petróleo e gás natural.
Os padrões são de alta prioridade para todos os envolvidos em dutos, seja na fabricação, instalação ou operação. A importância de qualquer diretriz, independentemente da organização que as recomende, é a segurança das pessoas e do meio ambiente.
MEDIÇÃO DAS DIMENSÕES DE TUBOS
A geometria de tubos, cilindros ou qualquer outra denominação que você prefira, é objeto de muitas interpretações variadas. O objetivo desta seção é fornecer um guia geral das dimensões comumente referidas por aqueles que trabalham com tubulações.
Comprimento
Essa dimensão é a distância total entre uma extremidade do tubo e outra.
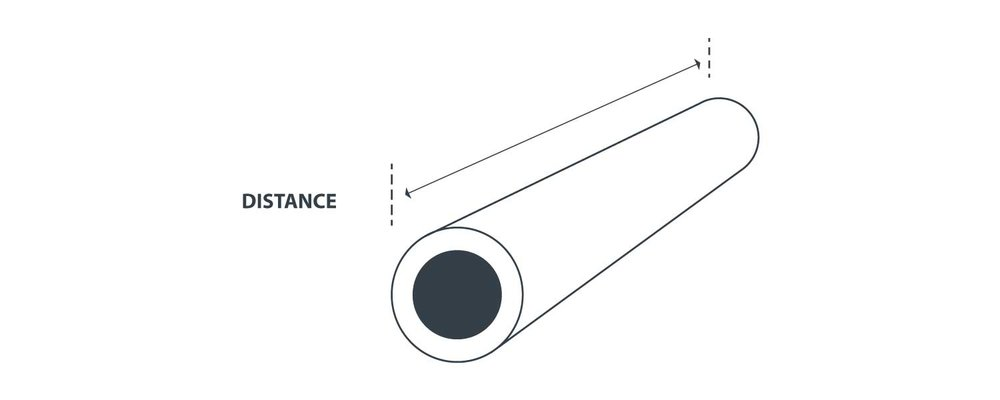
Diâmetro externo (OD)
Esta é a distância entre as bordas externas da extremidade do tubo.
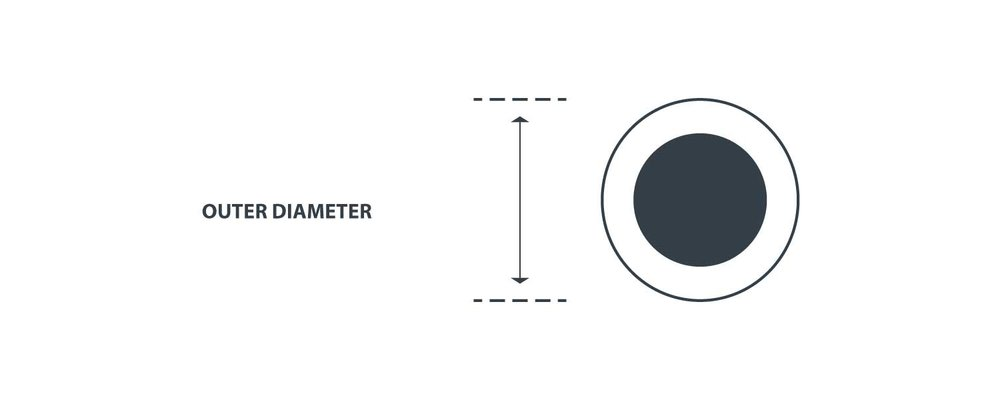
Diâmetro interno (ID)
O diâmetro interno é a distância entre as duas extremidades internas.
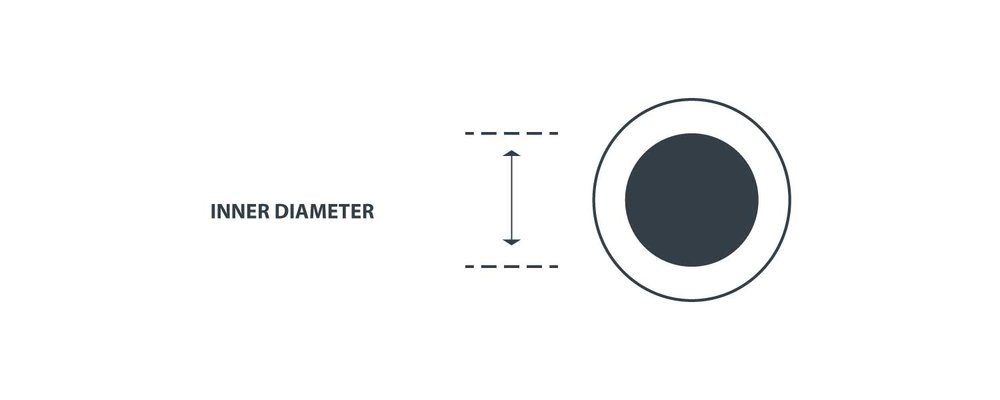
Espessura da parede (WT)
A espessura da parede do tubo é a largura total da parede.
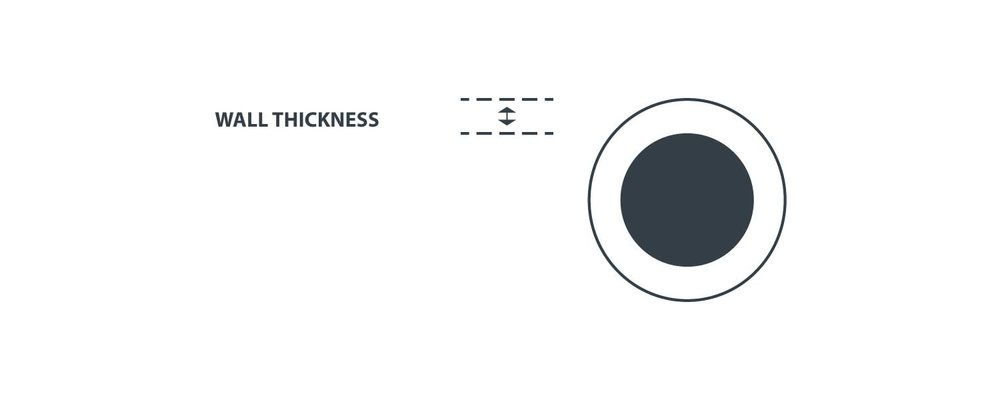
Normalmente, há falta de consistência em relação à referência das dimensões dos tubos. Por exemplo, nos Estados Unidos da América (EUA), as dimensões são citadas no sistema imperial (pés e polegadas), enquanto na Europa e demais partes do mundo é usado o sistema métrico(milímetros e centímetros). Embora possa não parecer uma preocupação significativa, considere a perda financeira de US$ 125 milhões para a NASA em 1999, quando a Sonda Climática de Marte, uma sonda espacial robótica, se desintegrou devido a unidades de medida mal comunicadas.
Maior clareza e um conjunto determinado de termos de geometria ajudariam a criar a terminologia dimensional necessária para a construção e operação consistentes de dutos.
Existem muitas outras medidas de tubos que abrangem as extremidades do tubo, incluindo a medição de perpendicularidade de extremidades (end squareness), retidão do tubo, dimensões das extremidades, ângulos, tipos de solda e juntas. Essas medidas são explicadas com mais detalhes em nossas páginas do blog.
FERRAMENTAS DE MEDIÇÃO
Tendo em vista que existem inúmeros aspectos de um tubo que podem exigir medições, existem muitas técnicas e ferramentas para realiza-las. Alguns métodos são básicos e fornecem resultados rudimentares, outros são muito mais complexos, mas podem fornecer dados precisos sobre qualquer dimensão específica do tubo.
O mesmo pode ser dito sobre as ferramentas de medição de tubos. Existem alguns dispositivos relativamente simples que são igualmente fáceis de usar.
- Ferramentas simples de medição de tubos
- Fita métrica
- Paquímetro
- Medidor de espessura
- Gabarito de perpendicularidade da extremidade do tubo
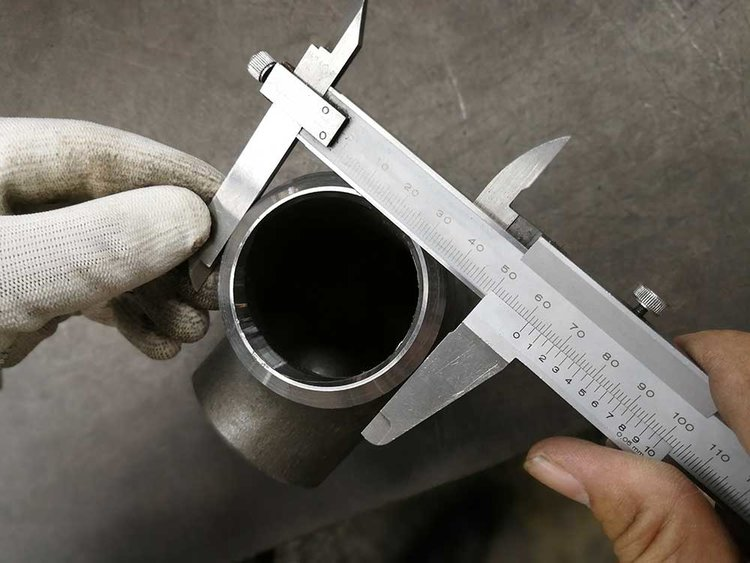
Muitas dessas ferramentas de medição de tubos são baratas e fáceis de aplicar, fornecendo resultados rápidos ao usuário. Apesar da natureza rudimentar desses métodos, eles podem ser suficientes para algumas aplicações de projetos de dutos. Medidas como o comprimento do tubo, diâmetro externo e interno, e espessura da parede podem ser obtidas facilmente.
Para situações em que as dimensões do tubo precisam ser obtidas com precisão garantida, onde se busca melhor repetibilidade ou maior precisão, ferramentas mais avançadas são necessárias.
Ferramentas avançadas de medição de tubos
Existem ferramentas para medir os aspectos mais complexos da forma de um tubo, incluindo:
- Perpendicularidade da extremidade do tubo
- Folga em soldas
- Formato do chanfro do tubo
- Grau de ovalição
- Circunferência interna de soldas
- Engate das extremidades
Ao contrário de suas contrapartes relativamente simples, essas ferramentas utilizam tecnologia inovadora, incluindo softwares avançados, para fornecer dados de medição mais completos e precisos.
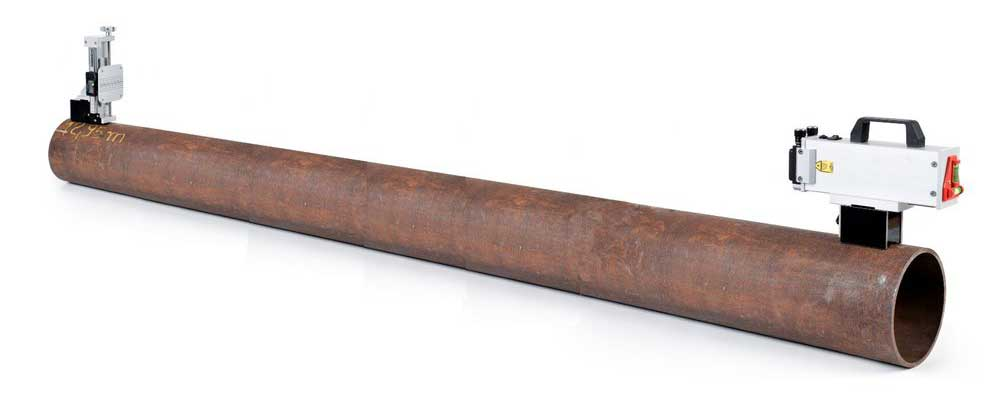
A tecnologia a laser, por exemplo, avançou ao ponto de poder ser usada para registrar milhares de medidas de uma extremidade de tubo, criando uma imagem com os pontos da geometria do tubo. Esses dados podem então ser analisados em um computador usando software dedicado de medição de tubos.
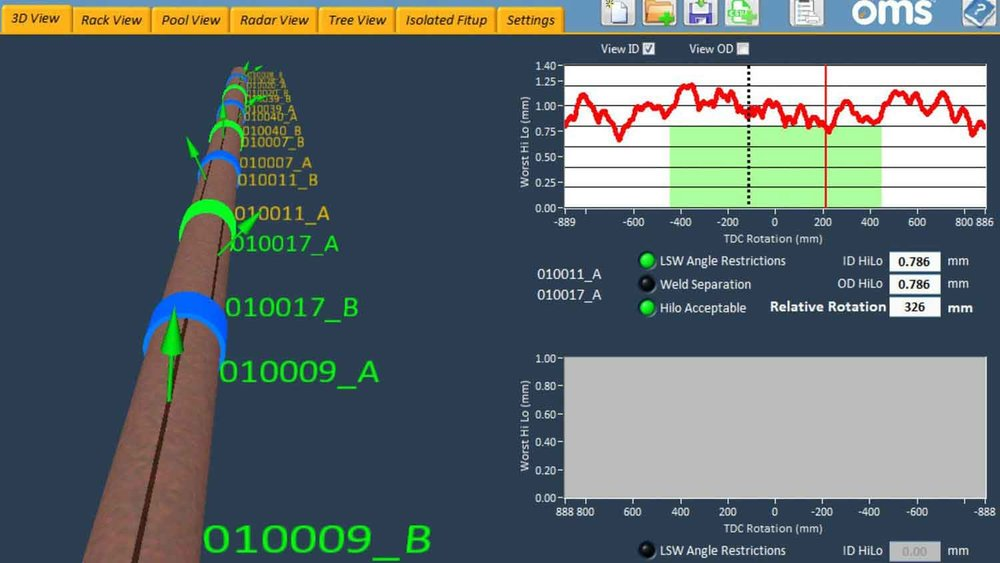
A análise dimensional precisa de um tubo pode ser útil em situações em que o alinhamento do tubo, ou encaixe, como é frequentemente chamado, é importante. A precisão com que um tubo é alinhado para oleodutos submarinos projetados para transportar petróleo bruto de volta para uma refinaria em terra é crítica.
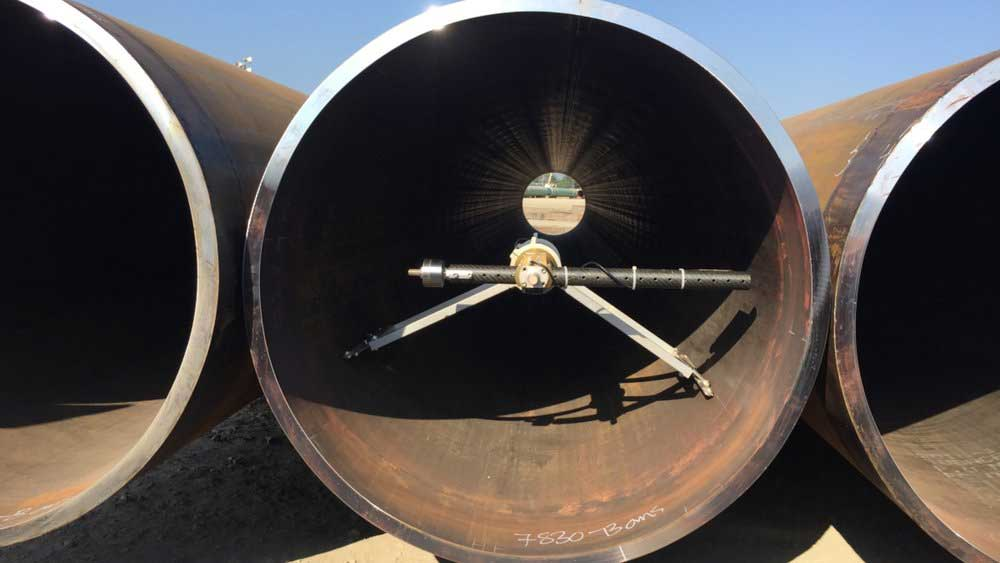
ALINHAMENTO DE TUBOS
O alinhamento de tubos é o processo de alinhar duas seções de tubo, geralmente uma extremidade com outra extremidade, em preparação para a soldagem e criação de uma seção mais longa de um oleoduto.
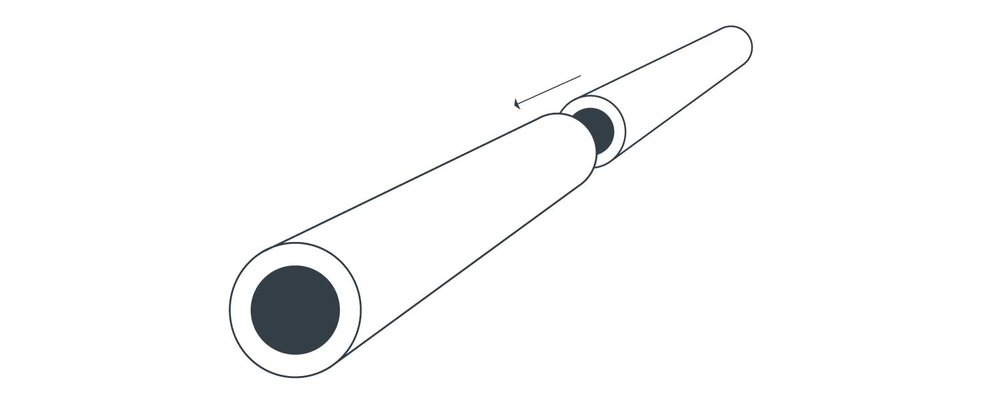
Apesar dos padrões de fabricação de tubos melhorarem com a tecnologia, o problema-chave é que:
- Os tubos nunca são perfeitamente redondos
- A espessura da parede do tubo nunca é constante
- Os comprimentos dos tubos raramente são consistentes
- Os tubos raramente têm geometria paralela
- Os tubos frequentemente têm imperfeições
Os tubos, e especificamente as extremidades dos tubos, muitas vezes parecem perfeitamente redondos aos olhos humanos, mas na realidade são frequentemente imperfeitos. Devido aos processos de fabricação, transporte e instalação, os tubos estão sujeitos a uma quantidade considerável de impactos. Isso pode fazer com que fiquem “fora de forma” com:
- Formato oval ao longo do comprimento e nas extremidades
- Amassados, arranhões, corrosões e escoriações na parte externa e nas extremidades
- Espessura inconsistente ao longo do comprimento e nas extremidades
O fato é que os tubos raramente são produzidos de forma consistente o suficiente para alcançar um alinhamento perfeito para soldagem. Isso não significa que um alinhamento perfeito seja necessário como padrão, na verdade, há inúmeras situações em que uma solda simplesmente precisa ser “suficientemente boa” para ser aprovada por um inspetor e cumprir os códigos de soldagem do projeto. Por exemplo, tolerâncias para oleodutos em áreas pouco habitadas e remotas são menos propensas a serem sujeitas às mesmas especificações rigorosas de um projeto de instalação de oleodutos submarinos.
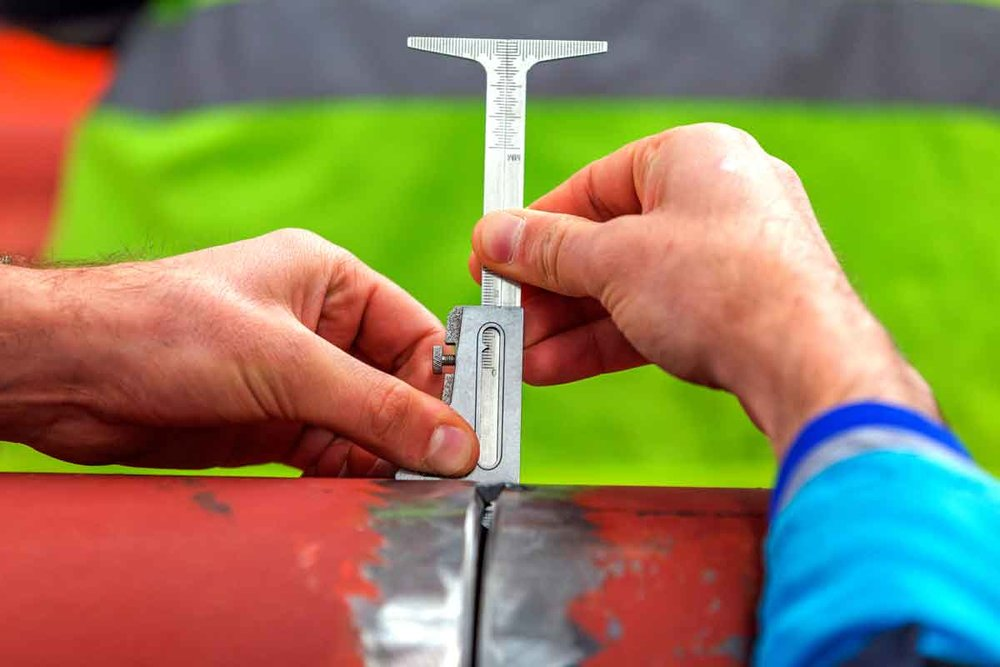
O alinhamento preciso de tubos é fundamental para situações em que o oleoduto provavelmente estará sujeito a pressão intensa, líquidos ou gases corrosivos, correntes como as encontradas no fundo do mar, risers rígidos em catenária(SCRs) ou juntas críticas de oleodutos, como emendas de trechos de tubulação.
INTRODUÇÃO À SOLDAGEM DE TUBOS
A prática de soldagem se estende muito além dos tubos para outras áreas da indústria, mas aqui abordaremos brevemente a soldagem de tubos para o setor de energia.
Tubos soldados devem resistir ao peso e à pressão do fluido que eles transportam, bem como às condições externas onde o oleoduto está situado. A maior resistência necessária dos tubos torna a soldagem um desafio para os engenheiros que têm que trabalhar com eles. Para aumentar a confiabilidade e a lucratividade nessa indústria, são necessárias técnicas eficazes de soldagem para esses materiais.
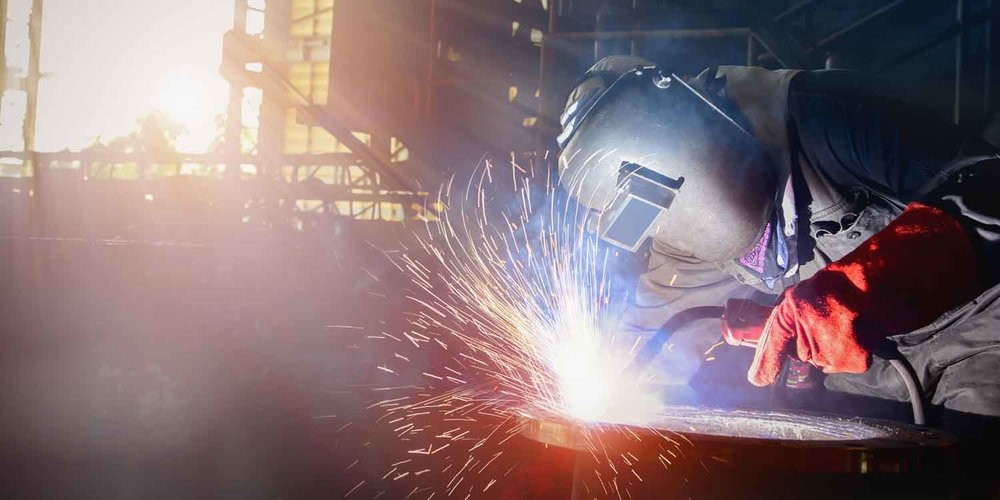
Entre 2014 e 2019, estima-se que 270.000 quilômetros de dutos tenham sido instalados a um custo de 216 bilhões de dólares. A demanda por dutos mais seguros, confiáveis e produtivos está aumentando, especialmente no setor de energia. Mas esse requisito surge em um momento em que há necessidade de dutos de diâmetros maiores, mais fortes e econômicos. Infelizmente, esses dois conjuntos de requisitos comprometem um ao outro. Quando você pensa em aumento de segurança ou durabilidade, pode traduzir isso como “preciso de tubos com paredes mais espessas”. Quando você quer reduzir os custos de instalação de tubos, provavelmente pensa em “preciso de tubos mais baratos”. É fácil ver como as necessidades da indústria nem sempre estão alinhadas com o que pode ser alcançado. A inovação pode desempenhar um papel fundamental na solução desses problemas.
Existe uma correlação clara entre a qualidade das soldas e o desempenho de um oleoduto. Soldas de alta qualidade resultam de um bom alinhamento das extremidades dos tubos. Se o desempenho de um tubo depende da qualidade das juntas ou soldas, e boas soldas resultam de um bom alinhamento, a resposta é bastante óbvia. Um melhor alinhamento das extremidades dos tubos contribui diretamente para soldas de alta qualidade, o que leva a um melhor desempenho do oleoduto.
Embora isso possa parecer óbvio, não é amplamente reconhecido pelos proprietários de oleodutos e pelas pessoas encarregadas da instalação.
Existem várias técnicas de soldagem de tubos, incluindo:
- Soldagem com eletrodo revestido (MMA ou MMAW)
- Soldagem com eletrodo metálico revestido (SAW ou SMAW)
- Soldagem com arame tubular (GAW ou GMAW)
- Soldagem com arame tubular com fluxo (FCA ou FCAW)
O procedimento de soldagem de tubos escolhido depende da escolha do tipo de tubo, do uso dentro do oleoduto e da localização onde será utilizado. Por exemplo, o processo de soldagem SAW (Submerged Arc Welding) é geralmente preferido para soldagem de arco em plataformas offshore, pois é mais adequado para a união de seções de tubos mais longas antes da instalação. Essas soldas devem ser capazes de suportar condições intensas de produção e condições extremas, especialmente em profundidades de água de até milhares de metros. Por outro lado, o trabalho com redes de tubos de utilidade publica, como esgotos, exigirá um processo de soldagem menos rigoroso.
As condições climáticas também podem afetar a escolha do tipo de solda, como calor extremo em condições de deserto ou temperaturas abaixo de zero em outras regiões. A soldagem de tubos é uma etapa crítica na construção de uma rede de oleodutos, pois soldas inadequadas podem levar a baixo desempenho ou, pior ainda, falhas e vazamentos no oleoduto.
FALHAS EM TUBOS E DEFEITOS DE SOLDA
Relatórios sugerem que entre 1998 e 2017, a corrosão foi responsável por cerca de 18% de todos os incidentes em oleodutos. À medida que a sensibilidade social e ambiental aumentam, a gestão da integridade de oleodutos, juntamente com o aprimoramento da tecnologia, está ajudando a reduzir essas ocorrências. No entanto, as falhas em oleodutos continuam sendo uma preocupação para todas as partes envolvidas na instalação de oleodutos. Os operadores de oleodutos devem aderir a padrões rigorosos para garantir que essas infraestruturas críticas sejam construídas e mantidas de forma a minimizar o risco de falhas em oleodutos.
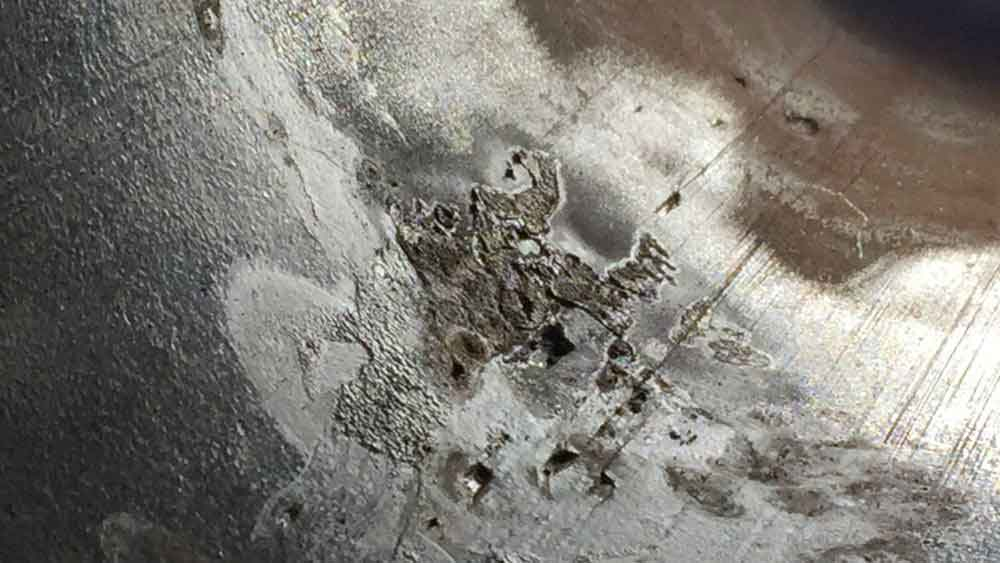
As falhas em tubos podem ocorrer por uma ampla gama de motivos, sendo a corrosão ou rachaduras talvez os problemas mais comumente encontrados. A corrosão é o processo pelo qual um metal se deteriora devido a uma reação eletroquímica chamada oxidação, ou ferrugem, como é mais comumente conhecido. A oxidação de tubos pode ser prevenida tomando medidas para limitar as condições que causam a corrosão, como selecionar o material mais apropriado para uso, adicionar inibidores de corrosão ao processo de tratamento de tubos, revestir os tubos e limpar os contaminantes internos.
A corrosão em tubos geralmente pode ser dividida em três tipos:
- Corrosão externa: geralmente decorrente de condições externas de temperatura, água ou pressão combinadas com o contato com materiais corrosivos, como solo ácido.
- Corrosão interna: resultante do transporte de produtos corrosivos ou pressurizados.
- Defeitos de corrosão: devido a características físicas, como forma ou formato, ou problemas resultantes do manuseio ou instalação.
Além da corrosão, estresse e rachaduras, a pressão ambiental e danos causados pela instalação ou escavação podem contribuir para a integridade de um oleoduto.
No entanto, tubos e outros ativos similares podem ser inspecionados em busca de corrosão e defeitos potencialmente prejudiciais, e uma vez identificados, corrigidos para garantir que a produção possa continuar sem interrupções. Esse tipo de inspeção de oleodutos pode efetivamente reduzir os riscos de um projeto durante a fase de instalação e também durante a fase operacional, onde verificações periódicas ocorrem rotineiramente.
Quando os tubos são soldados juntos, defeitos podem ocorrer por inúmeras razões. Soldas defeituosas podem comprometer significativamente as juntas, com efeito cascata comprometendo a integridade de todo conjunto.
Defeitos de solda em juntas podem ser causados por:
- Uso de materiais de qualidade inferior
- Processo de revestimento incorreto
- Atributos físicos, como amassados ou formato
- Técnica de soldagem inadequada
- Uso incorreto de ferramentas de soldagem
Defeitos de solda são normalmente descobertos quando são inspecionados usando raios-x ou equipamentos de teste ultrassônico automático (AUT). No momento em que soldas defeituosas normalmente são identificadas, a junta soldada provavelmente já passou por uma série de processos sequenciais. Esses processos podem ocorrer em terra ou a bordo de uma embarcação de instalação de dutos submarinos – depende da localização do oleoduto final – mas este último terá consequências financeiras significativas devido a atrasos e ao procedimento corretivo.
Se um defeito for encontrado nessa fase, as soldas problemáticas terão que ser removidas cortando-as, e então todo o processo terá que ser reiniciado. Ao inspecionar a solda em busca de um tipo específico de defeito de superfíci, durante as fases iníciais do projeto, é possível recuperar muito tempo perdido e economizar custos. Embarcações de instalação de dutos podem custar centenas de milhares de dólares por dia, então a economia é considerável.
Além disso, existem alguns tipos de defeitos que são menos sensíveis ou impossíveis de detectar nos processos posteriores, como coloração para soldas de liga resistente à corrosão (CRA), HiLo e porosidade.
INSPEÇÃO DE DUTOS
A inspeção de dutos é o processo de examinar um ativo usando técnicas não destrutivas (NDT), frequentemente para perda de metal, e ocorre mais comumente na fase de instalação ou durante a produção. Os dutos precisam ser inspecionados por várias razões, geralmente para garantir que o ativo esteja apto para o propósito e não apresente risco de falha. Por exemplo, uma inspeção de dutos pode ser recomendada por um inspetor como parte de um programa de garantia de qualidade, ou por um engenheiro de dutos em resposta a um problema conhecido com uma junta de tubo soldada. A inspeção de tubulações requer expertise em soldagem, uma certificação como o Certified Scheme for Welding Inspection(CSWIP) e, na maioria dos casos, compreensão das normas de conformidade.
O papel do inspetor é avaliar a condição das tubulações e antecipar problemas que possam se tornar questões mais significativas comprometendo a integridade da instalação de uma tubulação. A inspeção de tubulações requer o uso de técnicas como:
- Teste Ultrassônico (UT)
- Teste de Partículas Magnéticas (MT)
- Penetração Líquida (PT)
- Técnicas de teste radiográfico
Esses métodos podem ser utilizados tanto em terra quanto em offshore, e com ferramentas manuais e também com ferramentas de inspeção remota conhecidas como robôs ou crawlers. A maioria das localidades é acessível para humanos e permite o uso de ferramentas especializadas de medição e inspeção. Os crawlers robóticos são especialmente úteis quando é necessário acessar locais desafiadores onde a intervenção humana é limitada devido a restrições de espaço, ambientais ou de distância.
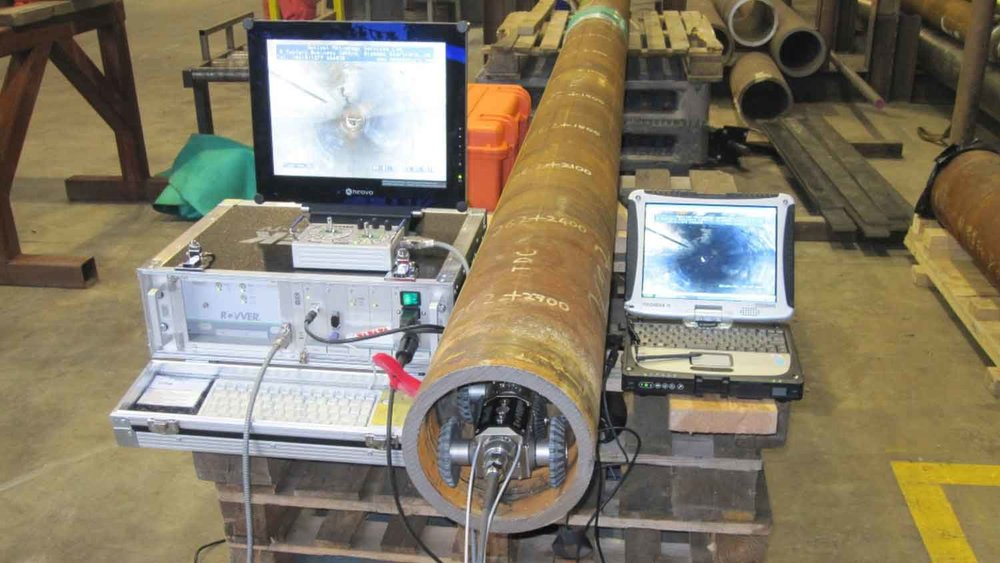
Unidades de inspeção robótica podem ser especialmente projetadas para se deslocarem em terrenos ou superfícies difíceis e em espaços onde temperatura, pressão ou substâncias químicas perigosas estão presentes, reduzindo assim o risco para a vida humana. Esses dispositivos podem ser projetados para trabalhar em linha com engenheiros de instalação de tubulações na linha de frente, e equipados com rodas ou esteiras. Uma variedade de ferramentas e tecnologias pode ser acoplada aos crawlers de inspeção robótica para realizar as tarefas desejadas, com dispositivos modulares para permitir personalização no campo.
Uma inspeção geralmente envolverá a verificação de:
- Alinhamento das tubulações – HiLo
- Integridade das soldas – penetração, concavidade
- Detecção de corrosão ou erosão
- Trincas ou fraturas
- Formato das extremidades da tubulação
- Espessura da parede
- Diâmetro
Compreender esses atributos requer habilidades especializadas e tecnologia sofisticada, incluindo tanto hardware para acessar a tubulação e realizar a inspeção, quanto software para interpretar os resultados.
Atualmente, há disponibilidade de hardware para medir tubulações e permitir a quantificação de aspectos como retidão, espessura da parede, diâmetro, bem como formatos de bisel. Algumas ferramentas fornecem resultados repetíveis e rastreáveis, que são cruciais para as especificações do projeto na maioria dos projetos modernos onde as tolerâncias de alinhamento das tubulações são críticas.
O software de inspeção de tubulações pode ser tão simples como imagens ou fornecer capacidades mais avançadas, como análise das extremidades dos tubos, onde varreduras a laser das extremidades dos tubos comparam medidas para permitir o ajuste mais eficiente possível de um grupo de tubos. Um alinhamento mais preciso das extremidades dos tubos antes da soldagem pode ter um efeito significativamente positivo na vida útil da solda, bem como na produtividade de uma tubulação, resultando em maior eficiência.
RESUMO
As tubulações evoluíram de tubos de madeira simples usados para transportar água de um lugar para outro para infraestruturas complexas de aço carbono que percorrem as profundezas dos mares. E assim como os dutos, a tecnologia usada para instalá-los, inspecioná-los e controlá-los também evoluiu. No entanto, estima-se que até metade dos dutos existentes nos Estados Unidos hoje tenham quase 50 anos de idade. Com uma estatística como essa, é difícil imaginar que os dutos do resto do mundo sejam muito diferentes em termos de idade.
Alcançar o desempenho máximo dos dutos é uma aspiração compartilhada por muitas das grandes organizações de energia que operam atualmente. A integridade é um aspecto fundamental de todos os dutos existentes e é uma consideração crítica para todos os operadores, independentemente do tamanho da empresa, localização ou comprimento das linhas que eles controlam. Manter a eficiência operacional, cumprir normas regulatórias e de segurança são amplamente considerados como o caminho para um desempenho máximo contínuo.
Garantir o desempenho máximo dos dutos deve incluir:
- Projeto e instalação corretos
- Uso de materiais de construção adequados
- Abordagem proativa para a manutenção preventiva
- Educação dos funcionários e sessões regulares de treinamento
O tema-chave para melhorar a produtividade nos dutos é um senso comum: investimento nas ferramentas, tecnologia e abordagem corretas para a tarefa em questão. O desenvolvimento de parcerias com especialistas em suas áreas, juntamente com a aplicação de novas ferramentas, podem ajudar as empresas de energia a avançarem com planos de projetos maiores e mais audaciosos.
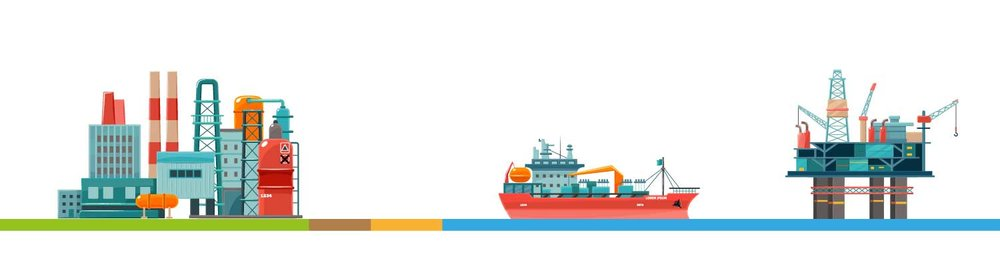
Para mais informações e orçamento, entre em contato hoje mesmo com um de nossos especialistas.